Reliable Strategies for Attaining Optimal Foam Control in Chemical Manufacturing
Reliable foam control is a crucial element of chemical production that can significantly affect production performance and item top quality. By comprehending the devices of foam development and choosing ideal anti-foaming agents, producers can take aggressive actions to mitigate excessive foam. Furthermore, the execution of process optimization strategies and progressed surveillance systems plays a vital role in preserving ideal operating conditions. The subtleties of these approaches can differ commonly throughout different applications, raising essential questions about best practices and real-world applications that merit additional exploration.
Comprehending Foam Formation

Surfactants, or surface-active representatives, decrease the surface stress of the liquid, helping with bubble security and promoting foam generation. Additionally, frustration or blending processes can boost bubble development, typically intensifying foam issues. The qualities of the fluid tool, including thickness and density, more impact foam actions; for instance, even more viscous liquids have a tendency to trap air better, leading to raised foam stability.
Understanding these essential aspects of foam formation is essential for efficient foam control in chemical production. By recognizing the problems that advertise foam advancement, suppliers can execute targeted methods to mitigate its negative results, thereby enhancing manufacturing procedures and guaranteeing constant item quality. This foundational understanding is crucial before checking out certain techniques for controlling foam in commercial settings.
Selection of Anti-Foaming Agents
When choosing anti-foaming agents, it is necessary to take into consideration the particular attributes of the chemical procedure and the sort of foam being created (Foam Control). Various factors influence the efficiency of an anti-foaming representative, including its chemical composition, temperature level security, and compatibility with other process materials
Silicone-based anti-foams are widely used because of their high efficiency and broad temperature variety. They function by decreasing surface tension, allowing the foam bubbles to coalesce and break more easily. However, they might not appropriate for all applications, specifically those entailing sensitive formulas where silicone contamination is a problem.
On the other hand, non-silicone agents, such as mineral oils or organic substances, can be useful in details circumstances, especially when silicone residues are undesirable. These representatives often tend to be less effective at greater temperature levels however can offer effective foam control in various other problems.
In addition, understanding the foam's beginning-- whether it develops from aeration, frustration, or chain reactions-- guides the selection procedure. Evaluating under actual operating conditions is crucial to ensure that the picked anti-foaming agent fulfills the special requirements of the chemical production process effectively.
Process Optimization Strategies
Efficient foam control is a vital facet of optimizing chemical production processes. To boost efficiency and decrease manufacturing expenses, makers should apply targeted process optimization strategies. One important technique includes readjusting mixing setups and rates. By fine-tuning these parameters, drivers can reduce disturbance, thereby reducing foam formation throughout mixing.
In addition, managing temperature level and stress within the system can considerably influence foam generation. Decreasing the temperature may minimize the volatility of particular parts, resulting in lowered foam. Also, preserving optimum stress levels helps in reducing extreme gas launch, which adds to foam security (Foam Control).
One more efficient technique is the critical enhancement of anti-foaming representatives at critical points of the process. Careful timing and dose can ensure that these representatives efficiently reduce foam without interrupting other process parameters.
Additionally, incorporating a systematic evaluation of basic material buildings can help recognize naturally frothing compounds, permitting preemptive steps. Lastly, conducting normal audits and process reviews can reveal inadequacies and locations for enhancement, allowing continuous optimization of foam control approaches.
Monitoring and Control Equipment
Tracking and you could try these out control systems play a vital function in maintaining optimum foam administration throughout the chemical manufacturing procedure. These systems are vital for real-time monitoring and modification of foam levels, making certain that production efficiency is maximized while decreasing interruptions brought on by extreme foam development.
Advanced sensors and instrumentation are used to discover foam thickness and elevation, supplying crucial information that informs control algorithms. This data-driven strategy enables for the prompt application of antifoaming representatives, guaranteeing that foam levels stay within appropriate limitations. By incorporating monitoring systems with process control software program, producers can carry out automated reactions to foam variations, minimizing the demand for manual intervention and boosting functional consistency.
Additionally, the assimilation of artificial intelligence and predictive analytics right into monitoring systems can help with positive foam monitoring. By analyzing historical foam data and operational specifications, these systems view it can anticipate foam generation patterns and recommend preemptive procedures. Normal calibration and upkeep of surveillance equipment are vital to make sure precision and integrity in foam discovery.
Inevitably, effective tracking and control systems are crucial for enhancing foam control, advertising safety and security, and boosting total performance in chemical production settings.
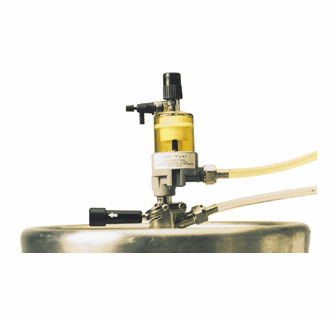
Situation Research Studies and Finest Practices
Real-world applications of surveillance and control systems highlight the importance of foam management in chemical production. A noteworthy study involves a massive pharmaceutical manufacturer that executed an automated foam discovery system. By incorporating real-time tracking with anticipating analytics, the center lowered foam-related production downtime by 30%. The data-driven method enabled for prompt treatments, ensuring consistent product top quality and operational performance.
Another excellent instance originates from a petrochemical firm that embraced a combination of antifoam agents and process optimization strategies. By assessing foam generation patterns, the company tailored its antifoam dosage, leading to a 25% decrease in chemical usage and significant price financial savings. This targeted method not only minimized foam interference yet likewise enhanced the overall security of the production process.
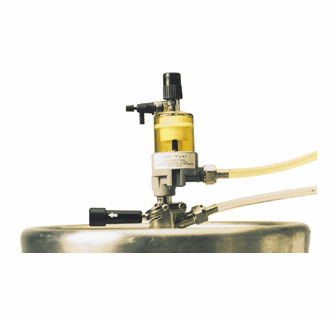
Final Thought
Finally, accomplishing optimal foam control in chemical production requires a detailed technique incorporating the choice of appropriate anti-foaming representatives, application of procedure optimization methods, and the combination of advanced tracking systems. Normal audits and training even more enhance the performance of these methods, fostering a society of continuous renovation. By dealing with foam development proactively, producers can significantly enhance manufacturing efficiency and item quality, eventually adding to more lasting and affordable procedures.
By recognizing the devices of foam development and selecting proper anti-foaming representatives, makers can take positive actions to reduce too much foam. The qualities of the fluid medium, including thickness and thickness, further influence foam actions; for example, more viscous fluids often tend to catch air more efficiently, leading to raised foam stability.
Understanding these essential facets of foam development is vital for efficient foam control in chemical production. By assessing historic foam data and operational specifications, these systems can forecast foam generation patterns and suggest preemptive actions. Foam Control. Normal more audits of foam control measures ensure that processes stay enhanced, while promoting a culture of proactive foam administration can lead to sustainable enhancements across the manufacturing range